Objectives
At the end of this chapter you should:
have a basic knowledge of the nature of metals;
have a basic understanding of what causes metals to corrode;
be able to take steps to minimise the corrosion of metals in your collections;
be able to determine whether corrosion is active or passive;
be aware of when and where not to apply chemical treatments to metals;
know the correct treatments for particular types of metal; and
be able to determine when it is necessary to seek professional assistance.
Introduction
Metals have played a significant part in human and technological development. This is reflected in the fact that two major periods in human history have been named after metals: the Bronze Age and the Iron Age.
Metals have been used—either in pure form or combined with other metals—to produce an enormous variety of objects, including weapons, tools, machinery, decorative art objects and jewellery. Because of the huge range of uses for metals, objects containing metal, or fully made from metals, are all around us. They make up a large part of many collections housed in museums, galleries and even some libraries.
But despite their apparent solidity, metals do corrode and can be vulnerable to physical damage. It is important that those responsible for the care of metal and metal-containing objects are able to recognise problems when they see them, and take steps to halt them.
Metal objects in collections
An enormous range of objects in collections are either made of metal or have metal components. Among them are:
- sculpture;
- jugs;
- armour;
- coins;
- cutlery;
- teapots;
- tools;
- aeroplanes;
- photographs;
- boats;
- hammers;
- scythes;
- traps;
- jewellery;
- buckles;
- rigging for boats;
- coatings on CDs;
- weaponry;
- clocks and watches;
- metal thread;
- signs;
- plates;
- buttons;
- pots and pans;
- zips, hooks and eyes;
- backings on mirrors;
- automobiles;
- badges and regalia;
- agricultural machinery;
- sewing machines;
- electrical equipment;
- scientific instruments;
- military machinery;
- screws and bolts;
- fittings on saddles.
Common metals
The metal objects in your collections will be made from a range of different metals, including:
- cast iron;
- wrought iron;
- bronze;
- brass;
- sterling silver;
- pewter;
- lead;
- tin;
- aluminium;
- gold;
- Britannia metal;
- Sheffield plate;
- steel;
- electroplated nickel silver;
- galvanised iron;
- stainless steel; and
- zinc;
The nature of metals
The atoms which make up metals are bonded in a way that is peculiar to metals. A metal becomes a solid at a certain temperature; and the atoms of the metal settle into a characteristic, well ordered configuration. In this configuration the atoms are fixed rigidly in relation to each other. The configuration is called a crystal lattice or a crystal.
Some of the basic qualities of metals include the following:
- they are good conductors of heat and electricity;
- high reflectivity when their surfaces are smooth;
- usually good ductility, that is, they are capable of being drawn out into wire or threads;
- good malleability, that is, they can be extended or shaped by hammering or by pressure with rollers; and
- mechanical strength.
Alloys
For centuries, the properties of metals—such as their appearance, strength, malleability and chemical reactivity—have been altered by combining them. These combinations are called alloys. For example, iron combined with carbon produces alloys such as cast iron and steel; whereas the alloying of chromium and nickel with iron forms stainless steel.
Similarly, copper can be combined with zinc, to form brass; and with tin, to form bronze.
Patina
The patina is a film of metal corrosion products which forms on the surface of an object as a result of:
- exposure to the elements; and
- deliberate steps taken to produce this effect. For example, sculptors often apply chemicals to the surface of a work, to produce a certain visual effect with the corrosion products.
Before any decision is made to remove this layer of corrosion products from an object, the nature of the object and its history must be considered very carefully. For instance, under no circumstances should the patina be removed from an ancient bronze sculpture, whereas a Victorian-era silver candelabra would have been highly polished and so should be cleaned of accumulated tarnish.
What are the most common types of damage?
Metals are vulnerable to physical damage and to chemical deterioration.
Physical damage includes:
- dents;
- wear of machine parts through repeated operation;
- wear of metal surfaces through excess polishing; and
- scratches. On highly polished surfaces scratches can be distracting and mar the appearance of the object; and on finely machined surfaces, for example in machinery, scratches can adversely effect the operation of the machine.
Chemical deterioration in metals is called corrosion. Physical damage to metal objects can leave them vulnerable to corrosion. For example, a scratch in tin plate leads to corrosion of the base metal.
Corrosion
The tarnishing or corrosion of metals will be your major problem if you are responsible for the care of metal items.
Gold, silver and copper are the only metals that are stable enough to be found in their natural metallic state. All other metals are more stable when combined with other elements, to form oxides, sulphides, chlorides, carbonates or mixtures of these.
There is a natural tendency for most pure metals to return to their more stable, corroded states.
Because of this, metal objects need to be protected from environmental conditions and pollutants which encourage corrosion.
In some cases—as the metal corrodes—the oxide film that forms acts as an insulating barrier, which slows the rate of corrosion to an acceptable level. Copper and aluminium are two metals in which oxide coatings form protective layers—called passivating layers. When iron corrodes, however, it does not usually form a protective film. Iron continues to corrode until no metal is left, unless some other protective coating is applied to protect it from the elements.
It is important to note also that corrosion builds up on top of the metal surface, and is often much thicker than the original metal. You may find that when you come to treat an object there is little or no original metal remaining; and removing the corrosion products could mean ending up with a much reduced object or none at all.
Causes of corrosion
Moisture and oxygen are required for metals to corrode.
Chloride ions, which are found in common salt— sodium chloride—can speed up the corrosion rate, and are also capable of penetrating protective oxide layers.
Fats, oils and sweat can also enhance corrosion.
Acids formed when air pollutants combine with moisture will attack metals. Outdoor monuments and sculptures are particularly vulnerable to this type of attack.
Relatively unreactive metals, such as copper and silver, can suffer significant corrosion if sulphide- containing materials are in the same environment as the metal.
These sulphide pollutants are usually associated with the breakdown of plant matter, and the decomposition of sulphur-containing proteins such as wool. A common pollutant is carbonyl sulphide—COS.
Dust absorbs moisture readily. So areas with a build-up of dust can have quite high local humidity—higher than the surrounding environment. Dust will absorb pollutants and other reactive materials as well.
Corrosion also occurs if dissimilar alloys and metals come into contact with each other. This type of corrosion is called galvanic corrosion.
Under these circumstances, the more reactive metal or alloy corrodes while the less reactive metal is protected. For example, if iron and copper were in direct physical contact in the presence of moisture and oxygen, then the iron would selectively corrode while simultaneously protecting the copper.
This problem can be overcome by avoiding direct contact between dissimilar metals. This will not be simple if the metals are components of the same object.
The oxide film which forms on particular metals acts as an insulating barrier or passivating layer barrier, slowing the rate of corrosion to an acceptable level. This type of passivation occurs with copper and aluminium.
When looking at the way in which artefacts have corroded and when deciding on management strategies, it is important to ask these basic questions: is it necessary to treat an object? or can the causes of deterioration be controlled?
For more information
For more information on the effects of humidity, dust and pollutants, please refer to Damage and Decay.
Common causes of damage
All the most common types of damage are caused by:
poor handling;
poor storage methods;
poor display methods;
inappropriate environmental conditions;
chemical interaction between the metals and other materials, including other metals; or
a combination of any of the above factors.
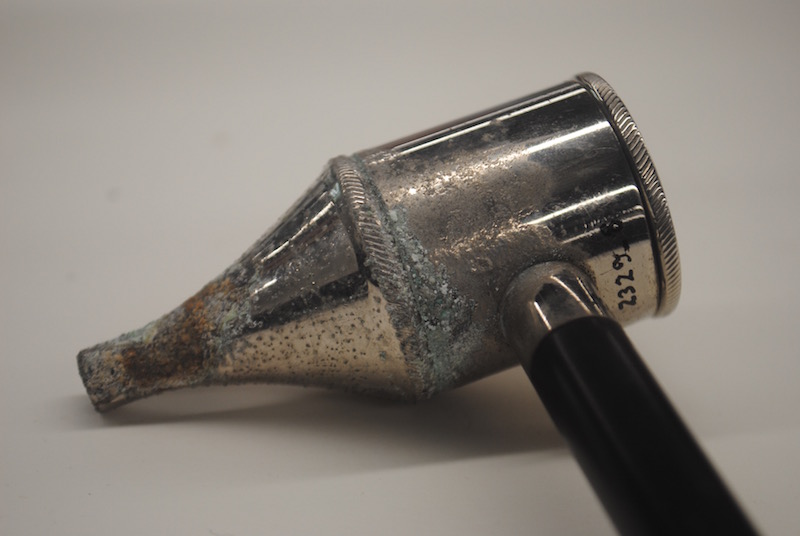
The following sections outline general storage and display principles for metals, as well as giving details of the problems, care and treatment of specific metals.
Handling, storage and display guidelines
When you are handling metal objects, particularly ones with polished surfaces, always wear clean cotton gloves or surgical gloves. This prevents the transfer of sweat and fats from the skin to the metal object, and helps reduce the risk of corrosion.
Always give your objects adequate support, and remember that metals can weaken over time.
Don’t lift metal objects by their handles. The joint between the handle and the object could be weak.
When displaying a hinged object open, take care to support it—so that the hinges are not carrying the weight of a part or all of the object.
Because some of the major contributors to the deterioration of metals are oxygen, water and air- borne pollutants, it is important to provide an environment which offers protection against these factors. This action can prolong the life of your metal objects.
Simple steps can greatly improve the longevity of objects. Steps such as:
wrapping objects in unbuffered, acid-free tissue;
placing them in acid-free boxes; and
storing them on painted—preferably baked enamel—metal shelving.
CAUTION:
Avoid chipboard or wood cabinets. These materials give off formaldehyde and organic acid vapours, which can accelerate corrosion.
If you have no choice about the type of shelving and you must use wooden shelves, we recommend you take the following steps:
coat wood with an epoxy or polyurethane finish to seal the wood;
paint chipboard with a solution of 400g of urea in 1 litre of water; and
allow time for proper drying and curing.
Do not seal objects in plastic bags, because the bags seal in moisture as well. This raises the relative humidity inside the bag, providing a microclimate which is favourable to corrosion.
CAUTION:
Avoid polyvinyl chloride—PVC—bags. They can give off hydrogen chloride, an acidic gas which will corrode most metals.
If you want to use plastic bags for storage, make sure you select polyethylene bags, and punch holes in the bag.
Store and display metal objects in environments where:
the temperature is stable—remember that fluctuations in temperature can cause the relative humidity to fluctuate;
relative humidity is less than 45%.
lighting levels are kept below 300 lux. Lighting levels should be lower if the objects are coated, because the light can adversely affect the coating; and
UV content is below 75 μW/lm.
For more information
For information about adverse environmental effects, please refer to Damage and Decay.
Corrosion can be stopped by removing oxygen or water from the local storage environment. Reasonably small, particularly vulnerable objects can be placed in a container with silica gel or an oxygen scavenger. Removing only one element of the corrosion equation, effectively halts corrosion—including bronze disease.
Guidelines for outdoor objects
If you are trying to prevent corrosion in an outdoor object:
bring the piece inside, or build a roof over it, if it is appropriate and possible. In most cases this won’t be possible;
look for areas where water can pool, and improve the drainage in these areas or remove water after rain;
don’t allow objects to sit directly on grass— raise them on a plinth;
don’t allow the object to sit in water;
don’t water the object when you are watering the garden—unlike the plants, it won’t grow; and
clean off bird excrement immediately—it is corrosive and will quickly etch the surface.
Metals in Australia\'s climatic zones
Metals in Australia’s climatic zones |
When considering the conservation needs of metals, the environmental conditions associated with the various climatic regions as well as those of the coastal areas must be taken into account. The moisture, salt and pollutant levels of the storage environment will have the greatest impact on the rates of corrosion, of metals. Metals corrode less in dry zones than in areas that have higher average relative humidity. Metal objects housed in coastal regions are at great risk of corrosion, if steps are not taken to minimise the impact of salt-laden air. |
Arid |
This climate is generally very dry, however, in arid areas, it is often very hot during the day and very cold at night. This wide fluctuation in temperature is matched by wide fluctuations in relative humidity, for example from 75%–20% in a day. Steps that can be taken include:
|
Temperate |
A temperate climate is considered a moderate climate, however, temperate climates tend to have a greater range of temperatures than tropical climates and may include extreme climatic variations. Steps must still be taken to overcome the extreme climatic variations which occur in these areas. High relative humidity conditions can be counteracted by:
|
Tropical |
These climates are characterised by heavy rainfall, high humidity and high temperatures. To counteract the problems associated with high relative humidity and generally high temperatures that characterise these regions the following strategies can be adopted:
|
Coastal Regions |
Coastal regions generally have more moderate climates than inland areas but they also have high levels of wind-borne salt. Consideration must be given to counteracting the corrosive effects of salty air. Steps which can be taken include:
|
Care of particular metals
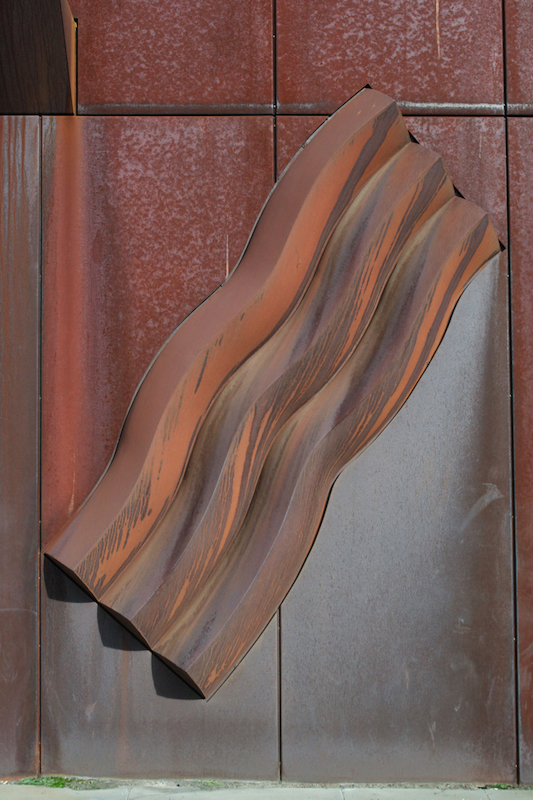
In this section, information is given about a range of metals. The information includes:
- a description of the metal and its alloys where applicable;
- the signs and main agents of corrosion of that metal and its alloys;
- methods of cleaning the metal;
- storage and display methods for each metal; and
- protective coatings that can be applied to objects made from that particular metal.
It is important to note that, while some of the methods for cleaning the metals are quite straightforward, others involve the measuring, mixing and application of reactive chemicals. It is strongly recommended that:
- you contact a conservator and discuss the risks involved in treating metal objects before you proceed;
- you do not treat an object unless you feel confident about carrying out the treatment;
- you do not treat an item if you are unsure about the type of metal with which you are dealing. A conservator can help you with this. It is also possible to carry out spot-tests to identify your metals;
- if possible, you practise the treatment on another piece of the same metal; and
- you attend a training workshop on the treatment of metals before attempting some of the more complex treatments.
It is extremely important that you are aware that some of the chemicals used in these treatments can also affect you.
CAUTION:
Thiourea is poisonous, is a suspected carcinogen and causes goitre.
Acetone can cause headaches, depression, nausea and dizziness when inhaled.
Industrial methylated spirits—IMS—is a mixture of ethanol and methanol and should be used with care. Ethanol can cause headaches, dizziness and nausea, and methanol is toxic and can cause blindness.
Ammonia can cause severe irritation to the skin and eyes, breathing difficulties, nausea and vomiting.
Disodium ethylenediamine tetraacetic acid EDTA—can be mildly toxic, and can affect unborn babies.
Citric acid is moderately toxic and irritating.
Petroleum spirit is flammable; it removes fats from the skin, and should be used with care.
Sodium carbonate can cause skin irritation and ulcers. If it is swallowed, it causes nausea, vomiting and diarrhoea.
If it touches skin, sodium hydroxide causes deep skin burns. If inhaled, it irritates the respiratory tract. If ingested, it can cause burning pain, diarrhoea swelling of the larynx and suffocation.
Silica gel in its granulated form can cause silicosis.
Protect yourself when working with these chemicals—wear gloves and masks. If you buy any chemicals to mix up your own cleaning solutions, ask for safety data sheets as well, and make sure that you store the chemicals safely.
You must also remember to take care when disposing of these chemicals—some of them cannot be flushed down the sink.
Silver
Silver’s lustrous appearance and relatively low natural abundance, its corrosion resistance and ability to be easily worked have made it a prized metal. Silver is often used for coins, jewellery and cutlery.
Most silver items found in Australia will be either sterling silver or plated silver.
Sterling silver
Sterling silver is the standard alloy used in jewellery and cutlery. It is made up of 92.5% silver and 7.5% copper. The addition of copper to silver increases hardness of the alloy, without any significant loss of lustre or colour.
Plated silver
The two common forms of plated silver are Sheffield plate and silver plate/electroplate.
Sheffield plate is made by fusion-bonding— sweating sterling silver to both sides of a copper or brass sheet; it is then worked to produce the desired object.
Silver plate or electroplate is formed when a thin layer of pure or sterling silver is deposited electrolytically on the surface of a base metal. Common base metals include copper, brass, nickel silver—an alloy of copper, zinc and nickel—and Britannia metal—a tin alloy with 5–10% antimony.
Electroplated materials are often stamped EPNS for electroplated nickel or silver, or EPBM for electroplated Britannia metal.
As commercial electroplating was developed in the 1840s, it is likely that a lot of the materials in the collections of local museums in Australia will be made of silver plate.
Signs of corrosion on silver
Silver artefacts tarnish if they are not kept polished. The silver surface changes through a faint purplish hue to a deep black. The tarnish is a layer of silver sulphide.
Artefacts excavated from underground or from the sea may be coated with grey silver chloride and copper corrosion products. If these materials have been exposed to sunlight, the surface will have a purplish tinge.
Cleaning silver
Clean silver only when absolutely necessary, and not as a routine treatment. This is because any cleaning removes minute amounts of silver.
Take great care to differentiate between tarnish and decorative treatments which are an inherent part of the object and which would be destroyed by cleaning. For example, a decorative treatment which should not be removed is niello, a black silver sulphide/silver copper sulphide that is used deliberately to highlight engraved sections of silver jewellery.
Avoid abrasive cleaners. They can cause fine scratching of the surface and remove small amounts of silver.
There are a number of proprietary brands of silver dip solutions available, which readily remove tarnish. These are usually made up of thiourea and acid mixtures. Silver dips should be used only when the object is badly tarnished.
If you decide to use a silver dip, apply the solution, or dip the object, only for as long as it takes to remove the tarnish.
Then rinse the object in hot water to remove residues, and dry it with a lint-free cloth. After drying, a final polish with a silver cloth will put a thin layer of corrosion inhibitors on the surface of the silver.
If Sheffield plate is in reasonable condition, it needs no further treatment other than being wiped with a silver cloth and displayed or stored under conditions of low relative humidity and away from wool.
Although there are commercially available solutions which gradually redeposit small amounts of silver on worn areas, these should be used only after considering the history and function of the object.
On no account should the object be replated. This completely devalues the object by removing the technological evidence of its manufacture.
Electroplated or silver plated objects which are in good condition, but on which the silver has been worn away to reveal underlying metal, can be restored by using a solution such as the one described above. This is a better way to rejuvenate the surface than the standard electroplating, which is a lot more costly and not always successful.
If the piece is in good condition, then it is better to maintain it in that condition, rather than continually cleaning it and wearing down the silver coating. Wiping with a silver cloth, followed by storage and display under conditions of low relative humidity and low pollution levels is the simplest method of protection.
Despite the best storage, display and care methods, all electroplated silver will eventually show pin-pricks of corrosion as the plating wears thin. Once the plating has been perforated, the underlying metal is prone to pitting corrosion; and the surface will gradually become covered with blotchy, black and green-blue areas of corrosion.
Simple care techniques don’t have much effect on this type of problem. It needs more complex treatment.
Immerse the object in a solution of 10g of thiourea and 50g of citric acid in 1 litre of water. This treatment will clean the object and remove the silver corrosion products.
After cleaning, the object must be placed in a diluted bath of sodium carbonate, 1% by weight in water, and left to soak for an hour or so to remove any citric acid from beneath the electroplate—to make sure that no further corrosion occurs. Follow this with a final wash in fresh, deionised or distilled water.
If the corrosion damage is not too severe, then the underlying metal can be re-touched using one of the silver solutions which redeposit small amounts of silver on worn areas. Finally, polish the object with a silver cloth.
CAUTION:
Check your chemical safety data sheets, and take the appropriate precautions.
Coating silver
There are lacquers available for coating silver objects, and these can significantly slow down tarnishing processes.
CAUTION:
These lacquers can be difficult to remove if they break down. And unless an even coating is applied, a patchy and blotchy tarnish may develop on the surface. Consult a conservator before coating your silver objects.
Storing and displaying silver
The general handling, storage and display guidelines apply to silver objects.
If you must place a silver object in a display case which has previously been shown to be corrosive towards silver, add zinc oxide or an acid-free zinc carbonate blotter to the base of the case to absorb the damaging substances. This will help to keep tarnishing to a minimum.
Alternatively, you could use the commercially available sintered zinc oxide pellets, or sachets of multi-metal vapour phase corrosion inhibitors.
Nickel silver
Most 19th and 20th century nickel silver objects will be found either as the unchanged copper-nickel- zinc alloy, or with a thin film of electro-deposited silver on the surface.
An easy way to identify nickel—as nickel plating or its presence in an alloy—is to look for the bright, lemon-green corrosion products which characterise nickel (II) compounds.
Australian coins minted before the introduction of decimal currency in 1966 contain significant amounts of silver. To remove tarnish from the imperial pre-1966 coins, follow the procedures for silver outlined above.
The corrosion products on Australian coins after the introduction of decimal currency are better treated according to the methods outlined below for copper as well as its alloys in the form of brass and bronze.
The treatment of electroplated nickel silver should follow the guidelines for silver objects.
Copper and copper alloys
Copper, a lustrous red-brown metal, is thought to be the first metal commonly used by humans. When alloyed with other elements, it provides a range of useful materials of widely different mechanical and corrosion-resistant properties.
The two main categories of alloys are:
those created when copper combines with zinc, to form brasses; and
those created when copper combines with tin, which are known as bronzes.
CAUTION:
Spelter bronzes which were popular from the 1850s to the early 1900s are not bronze at all, but a white, zinc-based metal to which various coatings have been applied, to give the effect of patinated bronze. Any attempt to chemically clean these objects renders them worthless.
Corrosion of copper
The types of corrosion products formed on copper and its alloys depend on the environment and the metal’s composition.
The most common corrosion products are copper oxides, basic copper sulphates and basic copper carbonates. These are generally stable, and protect the underlying metal from further corrosion.
The corrosion products are sometimes produced artificially—to give the attractive green-brown patina seen on outdoor bronze statues.
The passivating layers of copper corrosion products tend to break down in the presence of chlorides. Whether the chlorides are derived from the sea or from ground water, the overall impact—accelerated corrosion—is the same.
In a humid environment, the presence of chlorides in copper alloys can cause the development of the cyclic corrosion phenomenon known as bronze disease. This type of corrosion is characterised by the presence of a light blue-green, crumbly outgrowth on the surface. If this is brushed away, a pit will be evident on the surface. To determine whether an object is affected by bronze disease, consult a conservator.
It is important to note the difference between bronze disease and a natural patina. Many bronzes are formulated specifically to obtain a certain coloured patina. If you are not sure, consult a conservator before attempting any treatment. This is particularly important for Japanese and Chinese bronzes, and for bronzes from the Renaissance period onwards, as the patinas of these objects are intrinsic to the objects and should not be removed.
What causes the corrosion of copper?
Constant high humidity, pollutants such as sulphide gases, acids and careless handling causing physical damage can all cause deterioration of copper-based objects. In addition, heating and acidic cleaning solutions can etch the zinc out of brasses—leaving a copper-red discolouration on the surface.
Copper and copper alloys which have been buried or recovered from a wet site can suffer from the effects of chloride salts, resulting in the development of bronze disease.
Objects may also have special surface coatings, such as lacquers, which can be damaged easily by scratching or improper cleaning.
Cleaning copper and copper alloys
Items which are in good condition need only be wiped with a dry cloth.
Alcohol, preferably ethanol, may be used to remove greasy stains, but only after spot-testing to ensure there are no surface coatings that will be affected by this solvent.
If a badly tarnished copper alloy must be cleaned, immerse it in a solution of 10g of thiourea and 50g of citric acid in 1 litre of distilled water. This treatment will clean the object and remove the corrosion products.
The thiourea is an inhibitor which prevents any chemical attack on the metal itself. If thiourea is not used in the treatment solution, dissolved copper will be redeposited on the surface of the object, leaving a salmon-pink blush on the surface. This then has to be removed by polishing.
Leave the object in the solution until it is clean. This can take from several minutes to several hours, depending on the condition of the object.
You can speed up the treatment by brushing the surface, under running water, with a soft bristle brush, for example, toothbrush or soft Nylon, bristle brush. If necessary, a fine pumice powder can be used as a mild abrasive.
If this solution is not effective in removing tarnish, then the amounts of citric acid and thiourea used in solution can be increased to up to twice the strength.
The object must then be thoroughly washed to remove all traces of acid. This can be done under running water, or by immersion in baths of clean water.
If the object has been soaking for a considerable time or is porous, immerse it in a weak sodium carbonate bath—5g in 1 litre of water—in order to neutralise any remaining acid.
To ensure that washing has been effective, the pH of the surface of the metal object and that of the wash-water should be checked. The pH should be very close to 7, that is, close to neutral.
After washing, and before applying any protective coating, it is essential to make sure that the surface is free from grease and water. Any such contamination will show up later as corrosion areas.
Wear rubber gloves when cleaning and coating the artefacts.
If oven-drying at 100°C is not appropriate, the object can be dried by painting it liberally with acetone. The acetone drives out water in crevices and cracks, ensuring that the metal is fully dry.
The metal is considered dry when there is no longer any smell of acetone.
It is not appropriate to use acetone on composite materials or painted surfaces. To dry composite objects and painted objects, use a hair drier on a cold setting.
Note that this cleaning procedure will not produce a bright, shiny surface finish to the metal. If this is required, a proprietary metal polish can be used. Repeated polishing should be avoided, however, because it wears the metal surface.
CAUTION:
Check your chemical safety data sheets and take the appropriate precautions.
Coating copper and copper alloys
A protective coating can be applied, to maintain a clean, shiny surface on copper-based objects.
Lacquers and waxes are commonly used for this purpose. The patinas—excluding bronze disease— that form on bronze and copper objects are attractive and stable, and do not need a protective coating unless they are in a harsh environment.
Do not get dirt or fingerprints on the object between the cleaning and coating stages—any such contamination shows up later in the form of corrosion areas.
For coating, apply a microcrystalline-polyethylene wax preparation. An alternative coating is an acrylic lacquer containing a corrosion inhibitor. This is most satisfactory in preventing retarnishing of bronze and copper. Incralac is a commercially available lacquer which is available in a spray can or as a brush-on paint. This product can be removed with acetone.
Iron and its alloys
Iron is the most useful and abundant of metals and it is probably the most common metal found in the collections of local museums and historical societies. It has been known from prehistoric times and in its various forms—such as cast iron, wrought iron and various steels—it is the element upon which our present industrialised civilisation has been built.
Deterioration of iron and steel
Iron and steel, with the exception of stainless steel and other similar alloys, are readily attacked by oxygen when in the presence of moisture, forming rust.
Rust is a term used to describe non-specific corrosion products which form on the surface of degraded iron.
Unlike copper, the surface layers of iron corrosion products are not protective. They tend to accelerate corrosion of the metal by forming localised corrosion cells.
When an iron object is acquired, it should first be examined to determine the extent of deterioration and whether the corrosion is still active. If the surface is covered with yellow to brown droplets of moisture, it is a sign of severe corrosion activity, and indicates the presence of chloride salts. This necessitates a specialised conservation treatment to remove chloride ions. Please consult a conservator for more information about this treatment.
Many objects are covered with thick scales of rust—but there is often sound metal underneath.
Treatment of iron objects
Its future role, as either an object on display or in storage, will have a major impact on the treatment method.
To display an object in its working order, it may be that nothing needs to be done other than keeping it in a dry environment or coating it with an appropriate protective layer.
As with every metal type, there is a range of treatment options available; and the final decision will depend on the balance between aesthetics, economics and the function of the artefact.
Cleaning iron objects
Dirt, grease and loose or flaking rust must be removed before protective coatings can be applied to iron objects. Such deposits can be removed by chemical or mechanical techniques.
Chemical cleaning techniques include:
using soapy solutions to dissolve grease and remove surface dirt; and
immersing the object in an aqueous alkaline solution—caustic soda—to remove grease and paint. Concentrations in the range of 20–40g of sodium hydroxide per litre of water are normally used.
stripping corrosion products by immersing the objects in a solution of 50g of citric acid in water. While citric acid is relatively safe on most objects, care should be taken to ensure that cast iron, cast steel or spring steel, or combinations of these, are not left unattended for long periods, because these metals will actively corrode. Prolonged gas evolution—which you will see as bubbling— indicates that the iron surface is corroding. With harder alloys, this can also cause hydrogen embrittlement in which the hydrogen is generated within the metal and the stress of the gas pressure cracks the metal. Gas evolution can also result in pitted, weakened or destroyed objects.
CAUTION:
Do not use hydrochloric acid and phosphoric acid, because they will attack the underlying metal.
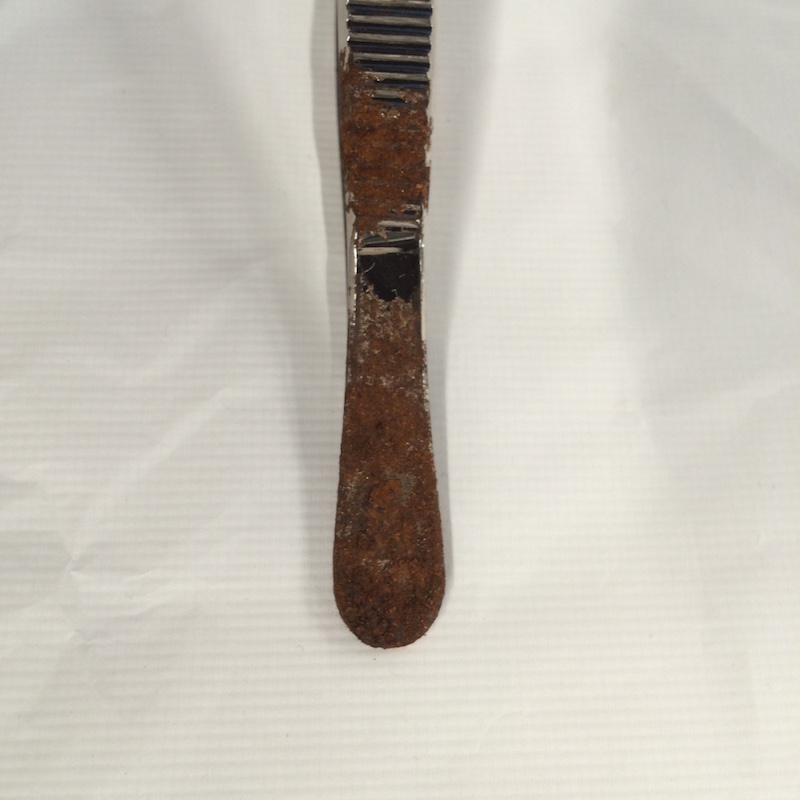
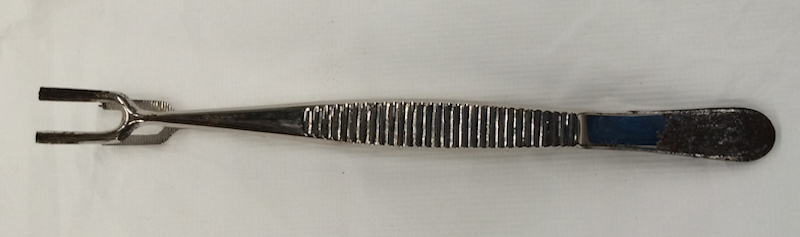
Plated iron
Iron may be plated with zinc, as in galvanised iron or tin, copper, chromium or nickel. These coatings protect the base iron sheet from corroding, and also provide a bright surface finish.
Corrosion of plated iron
Corrosion usually occurs after the breakdown of the surface plate. This exposes the iron, which then starts to rust.
Treatment of plated iron
To remove the rust, a citric acid solution containing an inhibitor can be used. The inhibitor is included to prevent any attack on the plating metal.
The solution is 10g of thiourea and 50g of citric acid in 1 litre of water. Thiourea is the inhibitor.
Test the solution on an inconspicuous area of the object, or on a scrap piece of the same material, before proceeding with the treatment.
Following removal of the rust, dry the object by dipping it in three successive acetone baths. At this stage, or earlier if there are no rust problems, the plate can be cleaned with industrial methylated spirits. Corroded areas can be removed with a mild abrasive such as pumice powder in methylated spirits.
CAUTION:
Check your chemical safety data sheets, and take the appropriate precautions.
Coating plated iron
If a bright surface finish is required after cleaning, a proprietary metal cleaner can be used as a once- only polish. The artefact can then be coated with a clear, acrylic lacquer.
Lead and pewter
Lead is a soft, grey metal, used mainly in combination with tin to form pewter. Because of toxicity problems associated with the use of pewter food vessels, the lead in pewter was replaced in the 19th century with antimony and some copper. Modern leadless pewters are usually alloyed tin and Britannia metal.
Corrosion of lead and pewter
The main corrosion product on lead and pewter is white-grey basic lead carbonate. This provides a deep, protective patina to the metal surface, which should not be removed.
If the pewter and lead have been in a low-oxygen environment and exposed to sulphide compounds, a rich, lustrous, grey-black patina of metal sulphides remains on the surface. These minerals are stable and should also not be removed.
Lead and pewter are particularly susceptible to attack by acids given out by wood. Acetic acid combines with lead and pewter to form lead acetates.
Both tin and lead are very soft and are susceptible to denting and scratching.
Cleaning lead and pewter
The stable patinas which form on lead and its alloys, the white-grey lead carbonate and the dark lead sulphide, should not be removed because they form protective layers which prevent further corrosion. Other corrosion products may require treatment.
Because it is difficult to obtain very mild abrasives, it is generally recommended that abrasives not be used to clean these soft metals. If, however, the white bloom on the surface of these metals is thin, the deposit can be removed from the surface using a one-micron-grade alumina powder mixed into a slurry polish.
If the white, bloom—an acetate layer—is pustular or thick, it is best removed by chemical or electrochemical reduction. These techniques are best left to conservators.
Thin layers of corrosion products can be removed by soaking the objects in a solution of 50g of disodium ethylenediamine tetraacetic acid in 1 litre of water. Avoid prolonged soaking because the dissolved oxygen can cause increased corrosion.
General cleaning can be carried out with warm water and a pure soap. Then rinse the object with fresh water, wipe it with methylated spirits, and polish it with a soft cloth.
A protective surface coating of microcrystalline wax may be applied after cleaning.
CAUTION:
Check your chemical safety data sheets, and take the appropriate precautions.
Storing and displaying lead and pewter
Lead and pewter are prone to attack from acetic acid and other organic acid vapours, which are found in poor-quality papers and some fabrics, and given off by various woods.
Storing lead-based objects in cupboards containing these materials contributes significantly to the deterioration. This type of degradation usually shows up when white, powdery crystals form on these materials.
Because lead and pewter objects are particularly susceptible to attack by acids emanating from certain woods, it is very important to store and display them in enamelled metal cupboards.
The general handling, storage and display guidelines previously described earlier in this chapter should be followed.
Tin and its alloys
Tin is a soft, white metal which is found in essentially pure form in some objects such as plates; but it is more commonly seen alloyed with lead in the form of pewter.
In the 19th and 20th centuries, tin was combined with a number of other elements to produce a range of alloys which were used principally for utensils and ornamental ware.
Typical examples are:
Britannia metal which is 93% tin, 5% antimony, 2% copper. It was developed in England during the mid-1700s in response to the threat to the pewter utensil industry from cheap porcelain. Old pewter was dull and, because of its lead content, was undesirable as a food container. Although the new alloy was brighter and stronger, it eventually lost favour as a metal for the production of household utensils; and
leadless pewter which is alloyed tin.
Corrosion of tin
Although it is normally quite stable, tin reacts slowly with the atmosphere to form grey, stannous oxide and finally stable, white to grey-black stannic oxide.
Many museum objects made of tin or its alloys are covered with a dull, grey coating of corrosion products. These form a protective patina. Unless very pronounced or unsightly, this patina should be retained.
Cleaning tin
Although tin objects are quite strong, careless handling will still damage their surfaces.
If an object must be cleaned, a pure soap in warm water can be used to remove dirt and grime. This should be followed by rinsing it with fresh water, wiping it with methylated spirits and then polishing it with a soft cloth.
Ask the advice of a conservator before treating badly deteriorated objects.
Aluminium
Most aluminium objects found in museum collections are alloys containing copper as a minor component. The addition of only 3% by weight of copper trebles the mechanical strength of the parent metal.
As aluminium corrodes, an oxide layer forms on the surface and protects it against further corrosion. Therefore, under normal environmental conditions the metal does not corrode to any great extent.
Deterioration of aluminium
If in contact with metals such as copper and iron, or in the presence of chloride ions from sea water, aluminium and its alloys will corrode appreciably.
Aluminium must never come into contact with mercury. Since mercury prevents the formation of the protective oxide patina, subsequent corrosion of aluminium is rapid.
Cleaning aluminium
Aluminium should be cleaned only with industrial methylated spirits, to remove dirt. Heavy deposits of oil, grease and petroleum products, commonly encountered on vintage car parts, can be removed by using kerosene or similar products.
If the metal is heavily stained or corroded, a 1% solution of phosphoric acid can be used. This will produce a mild, uniform etch on the metal surface which, after thorough washing and drying, should be left for a day to enable the protective corrosion film to reform through contact with the air. Consult a conservator for more information about this treatment.
Aluminium that has been contaminated with chloride ions can be treated by washing the corroded metal with a solution that contains ammonia and ammonium sulphate. This is a long term treatment which is best left to conservators. A corroded sea plane float, for instance, was only stabilised after soaking for a period of 12 months.
CAUTION:
Never use caustic soda to remove grease or paint from aluminium products, because it reacts vigorously with them. Don’t use abrasives on aluminium, because these can remove the protective oxide layer.
Coating aluminium
After cleaning, the aluminium surface may be coated with a protective, clear, acrylic lacquer. This protection is generally not needed unless the aluminium is likely to be affected by salt—for example, because of a sea-side location.
Gold
Gold has been used from the earliest times. It is yellow and lustrous, and the most malleable and ductile of all metals. As it is a rare metal, it has been used for jewellery and coinage.
Gold is often applied as a decorative surface coating—in the form of gold leaf for manuscript illumination and for gilt frames or tempera/fresco paintings, and as gold amalgam for gilding copper and silver. It is also alloyed with copper and silver to improve its mechanical properties.
Treatment of gold
Because gold is very resistant to corrosion, it usually requires only polishing with a soft cloth. No coating is required on pure gold; but if it is alloyed with copper or silver, a clear acrylic or nitrocellulose lacquer gives protection against retarnishing.
Alloys
All metals have physical properties—malleability, conductivity, strength, impact resistance and chemical reactivity. Their usefulness is determined by how these properties can be altered through alloying with other metals to produce a wide range of materials with tailor-made properties.
Alloying changes the corrosion resistance of the parent metal. Properties such as mechanical hardness and melting point also alter dramatically with alloying. The microstructure of alloys and metals is dependent on the rate at which they are cooled. This subsequently affects the rate of corrosion.
Mechanical working—such as hammering, drawing and rolling—also changes the microstructure of metals. If the stresses imparted to the metal are not relieved after fabrication, then stress corrosion can significantly diminish the service life of the materials.
An awareness of this behaviour in metals helps the conservator to respond in the most appropriate fashion to the various degradation problems that they find in collections.
Corrosion of metals
The overall driving forces of nature work to return metals to their stable oxidised states, that is, combined with oxygen, sulphates, carbonates, sulphides and chlorides. Unoxidised or native metallic element is produced when metals are unbound from their compounds with oxygen, sulphate, carbonate, sulphide and chloride. For this to happen there must be a sufficient driving force available through a high energy intervention. This intervention can be a carbon reduction or smelting. When metal ores are processed to produce metals, they start to corrode.
The primary property of electrical conductivity of metals is due to the dispersed nature of the electrons in the structure of the metals. When an external voltage is applied to a metal, the electrons flow. This very same useful property is the underlying cause for the corrosion of metals, because the voltage applied to the metal by the presence of oxygen in a moist environment will cause the electrons to flow irreversibly from the metal into the oxygen—to form an oxide coating.
A simple overview of corrosion
The corrosion of metals consists of two separate reactions:
an oxidation reaction; and
a reduction reaction.
To explain these reactions, it is necessary to give a simple overview of the structure of atoms. Atoms are made up of a nucleus which contains neutral particles called neutrons and positively charged particles called protons. Electrons, which are negatively charged particles, orbit around the nucleus of the atom. The number and activity of the electrons will determine how readily the atoms will react with other atoms. Many metals, because of the way their molecules are structured, can readily lose electrons. When they do this, they are no longer atoms. They are positively charged and are called ions. Because of the charge, ions are not stable and combine readily to achieve a stable, electrically neutral state.
An oxidation reaction is one in which an atom loses electrons. This can be represented very simply by the equation:
For example, copper—Cu—can be put into this equation. In an oxidation reaction:
- Cu Cu+ + e-
- It can be oxidised further: • Cu+ Cu2+ + 2e-
Copper is described as polyvalent, that is, it has different combining powers: a Cu+ ion needs one negative ion to achieve a stable state, while a Cu2+ ion needs two negative ions to form neutral compounds. Once these ions combine with other substances, they produce cuprous and cupric compounds respectively. For example, Cu2O is cuprous oxide or copper (I) oxide and CuO is cupric oxide or copper (II) oxide.
Iron and zinc are other examples of polyvalent metals.
In reduction reactions, atoms gain electrons. A simple representation of this would be:
These electrolytic reactions are used to produce solid metals from their ionic solutions. The negative ions can be supplied by a range of materials. For example, if the metal object is in a seaside location, chloride ions—Cl-—will combine readily with the metal ions.
They will also combine with:
sulphides—SO3-—sulphates—SO42—nitrates—
NO32-—from atmospheric pollutants; and
oxygen.
If the metal combines with oxygen, it forms a metal oxide on the surface of the metal. If this metal oxide is continuous, then the overall corrosion rate of the underlying metal will slow down and it will become passivated or protected.
Corrosion cells
Corrosion cells are small areas on metal objects where electrical differences are set up. Electrons flow between the charged areas, just as an electrical current flows between the positively and negatively charged electrodes of a battery.
A corrosion cell is an electrochemical cell which acts very much like a battery. The corrosion of metals consists of two separate reactions:
oxidation. The oxidation reactions are called anodic reactions; and
reduction. The reduction reactions are called cathodic reactions.
In an electrochemical cell the anodic, oxidation, half of the cell produces electrons as the metal is oxidised, while at the cathodic half of the cell, reduction occurs. The electrons are taken and held by the oxidising agent, which in aerated environments is oxygen.
In a corrosion cell, these reactions can continue in a cycle. The localised corrosion activity causes pitting in the metal.
The rate at which the electrons move out of the metal and across into the oxygen molecules is the principal factor controlling the overall corrosion rate.
Fats, oils and sweat
Organic acids—formed by the oxidation of oils and fats—are capable of attacking metals which rely on a protective oxide coating to produce a good corrosion resistance. To prevent this type of damage, avoid direct contact between the object and the source of the organic material. Some examples of this type of damage are leather objects with copper fittings. The gradual deterioration of old candle wax in leather- lubricating oils leads to organic acids penetrating the protective copper oxide film, and reacting with the underlying metal—to form outgrowths of bright green organic copper compounds.
Human sweat on metal objects causes corrosion. Bacterial reactions with sweat can produce sulphides as metabolic by-products, and convert inherently inert sulphate ions into reactive sulphide ions.
Uneven coatings of oil—from sweaty hands for instance—can alter the ease of access of oxygen to metal surfaces. This has two major effects. It hinders the formation of passivating layers of corrosion. It also alters the relative reactivities of areas of the metals; and so it causes one part of the metal to corrode at the expense of another.
Acids
Inorganic acids such as hydrochloric acid—derived from the decay of plastics like polyvinyl chloride— and nitric and sulphuric acids—derived from air pollution—will attack metals which are either in the same storage environment as the plastic or in the open air.
Anything that prevents direct contact between the metal surface and acidic solutions helps to prolong the life of the object. Therefore, vapour phase inhibitors, lacquers, waxes and other coatings minimise the damage from air pollution. The filtering of external air also greatly helps to minimise corrosion damage.
Sulphide pollutants
Normally unreactive metals such as copper and silver can suffer significant corrosion in the presence of sulphide ions. Common sources of sulphide ions are:
- hydrogen sulphide—H2S—from the anaerobic decay of plant material; and
- carbonyl sulphide—COS—from the degradation of sulphur-containing proteins, such as those found in wool.
Base metals such as zinc and tin are also significantly affected by sulphide pollution and/or contamination. Small concentrations of sulphur compounds in damp, oxygenated conditions cause corrosion. The resulting metal sulphides can often form a protective patina, as in the case of tin sulphides which protect pewter objects.
Adsorption of the sulphur-containing species is an essential step in the overall corrosion process and any factor which inhibits adsorption helps minimise attack on the metal. Therefore, adsorption of organic materials, such as vapour phase corrosion inhibitors, greatly decreases the corrosion rate.
Electroplate
The principal function of electroplating is to make a cheaper metal look like silver. The physical properties of the materials are dominated by the underlying parent metal or alloy.
When an object is being electroplated, it becomes part of an electrolytic cell, as if it were part of a battery. The object is the negative electrode—that is—the cathode. The anode—or positive electrode—is usually made of pure silver. During the electroplating process, the object is placed in a solution containing silver salts—for example silver cyanide—and a direct, electrical current is passed through the object. As this happens, the object becomes coated with a layer of pure silver. At the anode, the silver is oxidised to produce silver ions, which replace the silver in the solution.
If an inert anode such as stainless steel or platinum is used, the bath would need regular replenishment of the silver salts, to keep the same operating conditions in the plating bath.
If a silver/copper alloy layer is required, then the appropriate combination of silver and copper salts is dissolved, and the corresponding alloy is used as the anode.
Zinc carbonate blotter
If woven charcoal cloth or sintered zinc oxide pellets are not available or easy to obtain, then zinc carbonate can be used as a simple and very effective treatment against the adverse effects of sulphur pollution.
Sheets of acid-free blotting paper are immersed in a bath of a soluble zinc salt such as 10g of zinc sulphate in 1 litre of water.
Once the blotter is wet, a solution of 20g of sodium carbonate in 1 litre of water is poured into the bath, producing a white, cloudy solution of zinc carbonate.
The blotter is removed from the bath, and dried under pressure—to prevent cockling.
When dry, it can be placed underneath textile coverings in the base of a display case, or rolled up and placed in a support beneath a raised display platform within the display case.
This simple treatment has prevented the tarnishing of silver objects for a period of six years in a display case which has not been opened to release pollutant build-ups.
Brasses
The addition of varying amounts of zinc—Zn—to copper—Cu—produces a wide range of industrial brasses of differing physical and mechanical properties. These include:
gilding metal. The addition of only 5% zinc produces this alloy, which is commonly used as an artificial gold in decorative uses;
red brass: 85% copper/15% zinc. In this alloy, the underlying red colour of copper is still present;
yellow brass: 65% copper/35% zinc. The addition of more zinc hardens the alloy and changes the colour. This alloy is used for a wide range of industrial purposes, such as hinges, taps and valves; and
muntz metal: 60% copper/40% zinc. This alloy has a variety of uses, including sheathing for wooden sailing vessels.
In order to improve the ease of machining, varying amounts of lead are added to the hard brass alloys. Brasses containing more than 5% lead are self- lubricating, a very important factor for bearings and other similar objects.
Bronzes
When copper is alloyed with tin as the major additional component, different types of bronzes are formed. Bronzes can have significant differences in reactivity towards oxygen. The mechanical strength of the bronze normally increases with the addition of more tin, but the alloys become increasingly more brittle. Some of these alloys include:
- bell metal. With 20–25% tin, this is very strong, but very susceptible to cracking if struck with hard and sharp instruments;
- leaded bronzes: 80% copper/10% tin/10% lead. These are very robust and can be extensively cold-worked;
- statuary bronzes: 65–85% copper/10–30% zinc/2.5–5% tin. These are commonly used for casting; and
- china silver is an alloy of copper, tin, nickel and silver with 65% copper/20% tin/13% nickel/2% silver.
Bronze disease
Bronze disease is the name given to the type of corrosion of copper and its alloys in which light blue/green, pustular outgrowths form on the surface. It is due to the breakdown—by chloride ions—of the passivating layers of corrosion products which normally protect the surface of these metals.
The surface deposits tend to crumble and fall away when touched. As this loose debris is removed from the surface, a pitted surface is exposed directly under the corrosion mound.
Increased temperatures enhance this form of corrosion. A detailed description of the fundamental processes involved in the bronze disease cycle is given in an article by MacLeod, 1981.
This type of corrosion problem is most commonly found with bronzes—hence the name—less frequently in brasses, and occurs least frequently with copper itself.
Because of the relatively high background levels of chloride ions in much of the soil in arid Australia, the problems of bronze disease are encountered in objects that have been recovered from land sites, as well as those from a marine environment or coastal areas.
The corrosion problems are much worse when the materials are stored in high humidities. Under these conditions, a series of little dots and pustules will break out over the surface of an object. If the humidity is not lowered, or if some other form of treatment is not given to the object, then extensive corrosion and gross disfigurement of the object is inevitable.
One of the problems associated with bronze disease is that after the surface has been pitted, it is difficult to disguise that area, unless it is in- filled with coloured wax or some other suitable resinous material.
Treatment of bronze disease
The main aim of treating bronze disease is to remove all of the chlorides from the object.
This is done simply and effectively by immersing the object completely in a solution of 10g of sodium carbonate and 10g of sodium bicarbonate in 1 litre of distilled or deionised water.
A first wash of two to four months, followed by a second wash of four to six months in the solution is normally sufficient.
If the object originally had a bright metal surface, this treatment will produce a green-brown patina which is attractive and stable.
If a clean, metal surface is desired, the patina can be removed after treatment—using the citric acid stripping process or by polishing.
This method is effective for all cases of bronze disease, but the time required varies greatly from object to object.
Remove any protective coating on the object before treatment.
This treatment should be carried out by a conservator, or in close consultation with a conservator.
After removing the chlorides, apply a finishing treatment. Wax impregnation, a coating with benzotriazole or a coating with Incralac are commonly used.
Benzotriazole is one of a number of corrosion inhibitors for copper and its alloys. The reaction mechanisms are complex, but the primary protection is due to the formation of a very stable complex with copper, which protects the metal from further corrosion. Benzotriazole displaces chloride ions from cuprous chloride—this overcomes one of the fundamental causes of accelerated corrosion.
Microcrystalline/polyethylene wax
This is a good recipe:
100g of microcrystalline wax
25g of polyethylene wax
230g of white spirits
Melt the waxes together and stir well to make sure they are mixed thoroughly. Quickly pour the molten mixture into the white spirits and stir it constantly while it cools. This makes a smooth, white paste. The sheen of the resultant wax film can be altered by varying either the grades or the proportions of the waxes used. When it is dry, the wax can be polished, for a shiny finish, or left untouched for a matt finish. If subsequent treatment is be necessary, this wax can be removed with white spirit.
Iron and steel
The most important alloying element for iron is carbon—because it combines to form a diverse range of alloys, including wrought iron through to steels and cast iron.
In cast iron, carbon can exist as discrete phases or minute areas of graphite, in a variety of physical forms. Because of the differences in the hardness and chemical reactivity of the various phases, steels and cast iron are subject to localised corrosion—one phase is selectively corroded while another is protected. This is a form of internal galvanic corrosion.
The addition of other metals such as nickel and chromium result in the wide range of stainless steels, which are hard and chemically durable alloys. These alloys corrode to form protective coatings of chromium oxide/nickel oxide, and transform iron into a much less reactive metal with a much wider range of uses.
Adding elements such as molybdenum further improves the corrosion-resistance properties of the stainless steel alloys in chloride solutions.
Bentonite paste
Bentonite paste is made by sprinkling bentonite powder into a prepared solution of the alkali or acid, and mixing it into a paste. The concentrations of acid and alkali in the paste are usually higher than if a corresponding solution was being used.
For example, an 8% solution—that is, 80g per litre—of alkali and a 10% solution—that is, 100g per litre—of citric acid are recommended. The paste can be applied directly to the area to be treated.
If the surface is not smooth, residues of the paste can become clogged, making it awkward to remove. To make removal easier, first place a piece of water-dampened tissue paper over the treatment area, and apply the paste on top. It is preferable to cover the poultice of paste with cling wrap, to prevent it drying out.
Repeated applications of the paste may be required. The paste can be removed by hosing the surface with water and scrubbing it with a bristle brush. Then dry the object fully.
Bentonite paste treatment is also recommended if solder joints or related fastenings are present, because these are also readily attacked by citric acid.
Chloride ions and aluminium and its alloys
The presence of chlorides in aluminium alloys containing copper is a problem because chloride ions:
- penetrate the protective oxide coating;
- cause aluminium pitting corrosion; and
- promote localised copper corrosion from within the alloy.
As the copper corrosion products move to the surface, they interact with the aluminium corrosion products and form a blue-green, copper-stained aluminium hydroxide corrosion matrix.
The real problem occurs when—as a result of electrochemical reduction by the parent metal— copper is redeposited in metallic form on the surface of the alloy. The redeposited copper acts as a cathode in a pitting corrosion cell.
The conservation problem is to remove a relatively unreactive metal deposit from the surface of a very reactive metal, while at the same time trying to remove the chloride ions.
One simple solution to the problem is to use a solution of ammonia and ammonium sulphate to wash away the chlorides and the metallic copper from the surface. This produces complex reactions, but is effective.
When a corroded sea plane float was treated this way, it took 12 months of steady soaking, scrubbing and cleaning to stabilise the corroded metal.
Spot-tests
Spot-tests are used to distinguish different metals which make up an alloy. Simple instructions and a list of the tests are provided, to help you identify metal objects in your collections. It is important to note that these tests are only qualitative in nature—they will not tell you the relative amounts of the different metals in an alloy.
General instructions
Do the tests in unobtrusive spots, because marks may be left.
Remove protective coatings such as lacquers and waxes, otherwise there will be no reaction and no identification can be made.
The test papers to be used with the electrolysis are best cut into triangles. They are easier to handle this way and, if cut reasonably small, will leave less of a mark on the metal object being tested.
When wet—but not soaking—with distilled water or salt solution, the papers should be shiny.
The alligator clip needs to be attached firmly to an area of reasonably solid metal.
The test paper in the tweezers should be put on the surface of the object, about 1cm away from the clip.
Don’t let the metal tweezers contact the surface of the metal. The electrical contact must be made through the wet test paper.
Rinse wet spots of electrolyte, for example, NaCl— sodium chloride—or other reagents with distilled water, and dry them.
The battery should be stored disconnected from the tweezers and clip—to avoid accidental discharging if the two should touch.
Tests for identifying metals in an alloy
Antimony—Sb
Procedure: dip a small piece of antimony test paper in diluted HCl—hydrochloric acid—and apply it to the object.
Results: the presence of Sb is indicated by an orange colour. The reaction is complete in five seconds on pure Sb using 2% HCl. Surfaces containing trace Sb will be much slower. Gold— Au—and silver—Ag—surfaces remain unaffected by the test. Lead—Pb—is slightly darkened, copper—Cu—and iron—Fe—corrosion products change colour slightly.
Copper—Cu
Procedure: wet a small piece of commercial test paper—Cuprotesmo—with distilled water and place it on the surface of the metal.
Results: the copper metal or Cu+ and Cu2+ ions cause the pale yellow paper to turn pink/purple. This test works particularly well on corroded or patinated areas, and leaves no trace of the test. On highly polished or new surfaces, the reaction is much slower.
Gold—Au
Procedure: dip a small triangle of plain, filter paper in a saturated solution of sodium chloride in water. Electrolyse for less than 15 seconds. Some darkening will probably be evident if copper is present. Leave the paper on the spot until it is slightly dried, to ensure that gold is on the surface of the paper. Then dip it into a mixture of 20% tin chloride—SnCl2—in 15%HCl.
Results: the paper turns black if gold is present.
Iron—Fe
Procedure: for corroded objects, dip a small square of dipyridyl test paper in distilled water and place it on the surface of the object. This leaves no visible effect on the object. For uncorroded objects, dip a long piece of dipyridyl test paper in NaCl saturated solution so that the paper is wet but not saturated—electrolyse. The paper should be long, to prevent confusion with any colour reaction which occurs with the steel of the tweezers.
Results: if iron is present, the white test paper turns red after several seconds—for corroded and uncorroded objects.
Nickel—Ni
Procedure: dip a small piece of nickel test paper into a saturated solution of NaCl. Electrolyse for about five seconds.
Results: on drying, the following colours may be observed: pink-red for nickel, brown for iron, green for copper and yellow for gold.
Silver—Ag
Procedure: wet a filter paper with 10% potassium chromate K2CrO4. Electrolyse for one second or less.
Results: if silver is present, a red silver chromate Ag4CrO4 forms in the spot of the metal. This mark, if small, can be polished off very easily.
Tin—Sn
Procedure: dip a small piece of filter paper in a saturated cacotheline solution—0.6% aqueous. When the cacotheline dries slightly, dip the filter paper in NaCl saturated solution. Electrolyse.
Results: if tin is present, the paper turns purple. Shiny surfaces become matte and dark after two second of electrolysis.
Zinc—Zn
Procedure: dip a small piece of filter paper in sodium hydoxide NaOH—5–10% solution—and apply the paper to the surface of the object for five to ten seconds. Electrolysis is recommended. When the sample has been absorbed in the filter paper, place this paper in the centre of a larger filter paper, making a wet spot. Wash this spot with successive drops of dithizone/carbon tetrachloride, CCl4.
Results: if zinc is present, the edges around the sport turn pink—not orange. Wipe off immediately any NaOH remaining on the metal of the object. This can be done with the same filter paper being used for the dithizone reaction. Shiny zinc surfaces may be slightly darkened or dulled after electrolysis. There is a small effect on some copper corrosion products, and the NaOH droplet causes a shiny spot to develop on lead.
If you have a problem relating to the care of metals, contact a conservator. Conservators can offer advice and practical solutions.
For further reading
Brown, B.F., Burnett, H.C., Thomas Chase, W., Goodway, M., Kruger, J., Pourbaix M., eds. 1977, Corrosion and Metal Artefacts—A Dialogue between Conservators and Archaeologists and Corrosion Scientists, NBS Special Publication 479, U.S. Department of Commerce/National Bureau of Standards, Washington, D.C.
MacLeod, I. D., 1981, ‘Bronze Disease: An Electrochemical Explanation’, ICCM Bulletin, VII, ICCM Inc, Canberra, pp 16–26.
Stambolov, T., 1985, The Corrosion and Conservation of Metallic Antiquities and Works of Art, CL Publication, Central Research Laboratory for Objects of Art and Science, Amsterdam.
Scott, David A., 1991, Metallography and Microstructure of Ancient and Historic Metals, The Getty Conservation Institute, The J. Paul Getty Museum in association with Archetype Books, Marina del Rey, California.
Scott, D.A., Podany, J., Considine, B.W., eds. 1994, Ancient and Historic Metals: Conservation and Scientific Research, Proceedings of a Symposium organised by the J. Paul Getty Museum and the Getty Conservation Institute, November 1991, The Getty Conservation Institute, Marina del Rey, California.
Self-evaluation quiz
Question 1.
Select the incorrect statement from the following:
a) damaged Sheffield plate may be repaired by electroplating;
b) moisture and oxygen enhance corrosion;
c) a protective oxide layer forms on the surface of copper objects;
d) microcrystalline wax gives good corrosion protection for iron objects.
Question 2.
Gloves should be worn when handling metal objects so that:
a) oils, fats and sweat are not transferred to the object;
b) the object is less likely to slip from your grip;
c) protective lacquers are not damaged by nails;
d) your hands are not affected by toxic corrosion inhibitors.
Question 3.
Silver cleaning should be carried out only when absolutely necessary because:
a) silver dip solutions are very expensive;
b) any cleaning solutions remove small amounts of silver;
c) cleaning solutions tend to accumulate in indentations and surface cracks;
d) evidence of historic usage may be lost.
Question 4.
Select the correct statement from the following:
a) copper is more susceptible to bronze disease than is brass;
b) bronze disease only occurs in objects recovered from the sea;
c) bronze disease can be treated with a citric acid/thiourea solution;
d) the presence of high concentrations of chloride ions leads to bronze disease.
Question 5.
The presence of brown droplets of moisture on an iron object indicates:
a) there are low levels of chloride ions in the metal;
b) the metal is being attacked by sulphide pollutants;
c) the metal has been buried in a low-oxygen environment;
d) corrosion reactions are still active.
Question 6.
Select the correct statement from the following:
a) wooden cabinets are preferred to painted metal ones for storing metal objects;
b) metal objects should be wrapped in unbuffered, acid-free tissue paper;
c) storage in plastic bags is acceptable as long as they are not made of PVC;
d) relative humidities greater than 45% are essential to help in the release of chlorides from metals.
Question 7.
Which of the following statements are correct?
a) The main corrosion products that form on lead are stable and protective.
b) Abrasives are recommended for the removal of most corrosion products from lead.
c) Use of ethylenediamine tetraacetic acid is effective in removing thin layers of corrosion products.
d) Microcrystalline wax may be applied to lead as a surface finish.
Question 8.
Which of the following statements is incorrect?
a) Aluminium may be cleaned with methylated spirits.
b) Caustic soda should be used to remove grease from aluminium.
c) Abrasives should be avoided for cleaning aluminium because they can damage the protective layer.
d) Chloride ions are potentially damaging to aluminium objects.
Question 9.
Citric acid may be used to treat:
a) cast iron, cast steel, spring steel and plated iron;
b) brass and bronze, but only if thiourea is added;
c) silver plate;
d) lead and pewter.
Answers to self-evaluation quiz
Question 1.
Answer: a).
Question 2.
Answer: a).
Question 3.
Answer: b).
Question 4.
Answer: d).
Question 5.
Answer: d).
Question 6.
Answer: b).
Question 7.
Answer: c).
Question 8.
Answer: b).
Question 9.
Answer: b).